Our EcoPulping technology optimises sustainable sources of lignocellulose to produce the pulp. The process uses lower temperatures than traditional pulping. It is virtually a closed water system, consuming less than 5% of the water throughput of conventional pulping. EcoPulping recovers valuable by products that can be used or sold.
Process Steps
Our process is simple when compared to traditional pulping, using up to 50% less energy with simpler equipment. EcoPulping is a biomechanical process involving cooking, refining, cleaning, screening and washing:
Yield
Depending on the raw material, the grade and the end use, the yield of EcoPulp is:
- 65-70% for unscreened wheat straw pulp
- 50-55% for cleaned and screened pulp
Installation Types:
EcoPulping plants can be installed at the front end of packaging mills, or as independent units close to sources of agricultural wastes. Installations can be as:
- An independent unit to produce marketable unbleached pulp, for example close to raw material source. In this instance the EcoPulp is sold and transported to the paper or packaging mills.
- A retrofitted installation to paper or packaging mills, where paper or packaging production can be integrated to the EcoPulping mill.
Commercial EcoPulping mills can be built for small size (20 TPD) up large (400 TPD) plants.
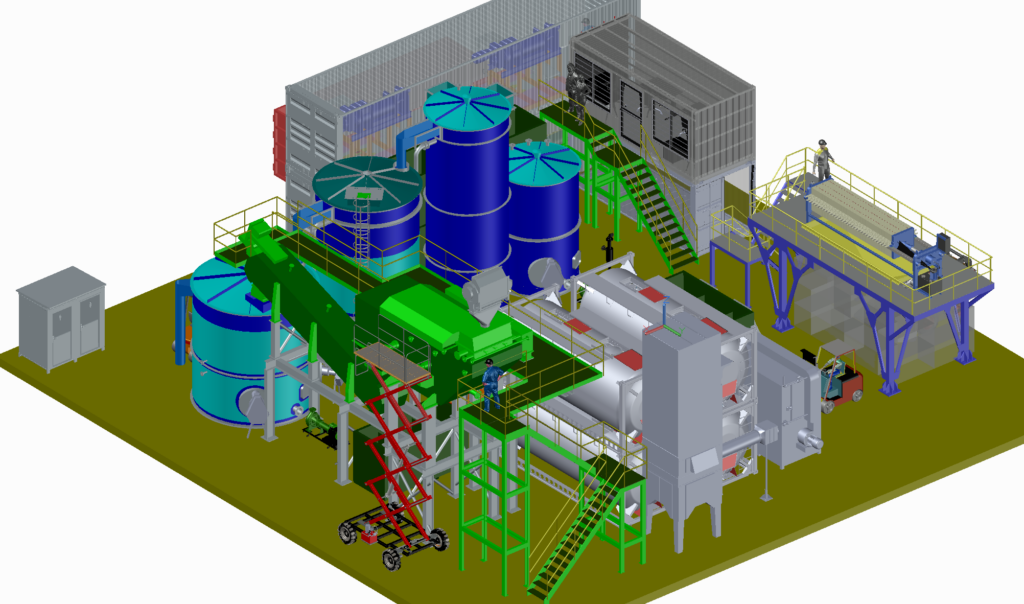
EcoPulping 20TPD